Process meter calibration is a crucial course of that ensures the accuracy and reliability of devices used
Process meter calibration is a critical course of that ensures the accuracy and reliability of instruments used to measure various parameters in industrial processes.
The main aim of calibration is to confirm and adjust the accuracy of process meters to ensure that they provide dependable and precise measurements.
Types of Process Meters:
Process meters embrace devices that measure parameters similar to strain, temperature, circulate, stage, pH, conductivity, and electrical alerts. Calibration is specific to the type of meter and the parameter being measured.
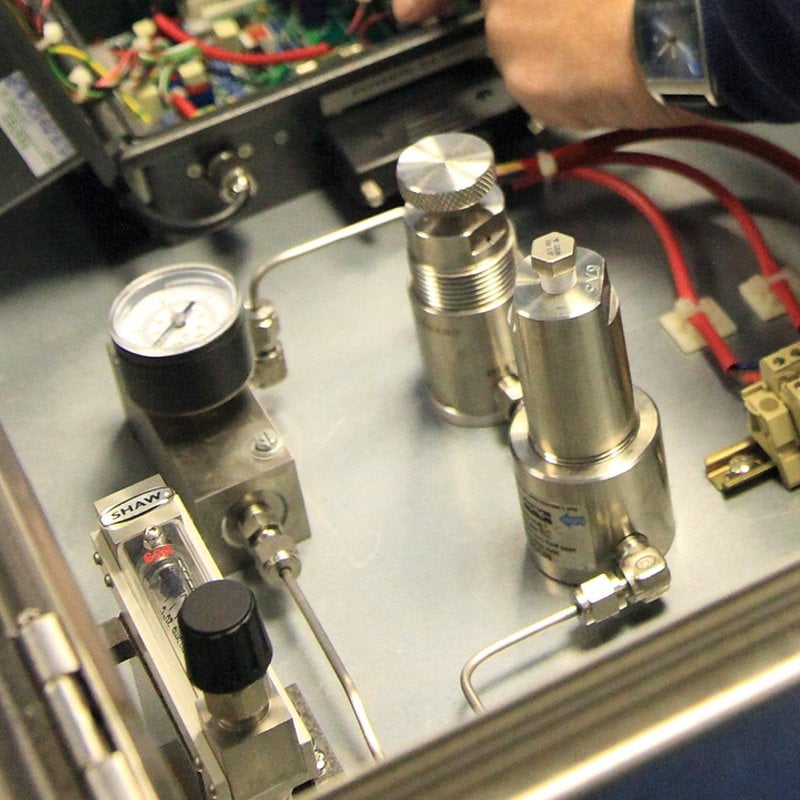
Calibration Standards:
Calibration is typically carried out utilizing standards, that are devices or devices with identified and traceable accuracies. https://ips-us.com/calibration/process-meter-calibration/process-meter-calibration-basics/ for comparison.
Traceability:
Traceability is the power to trace calibration measurements again to recognized nationwide or worldwide requirements. It ensures that the calibration process is reliable and follows a documented and verifiable path.
Calibration Procedure:
The calibration process entails comparing the readings of the method meter with the readings of the calibration standard. Adjustments are made if discrepancies are found.
Calibration Equipment:
Specialized calibration gear is used based mostly on the type of course of meter being calibrated. This may include stress calibrators, temperature baths, flow calibrators, multimeters, and other testing tools.
Calibration Interval:
Calibration intervals are established based on elements similar to business standards, manufacturer suggestions, and the criticality of the measurements. Regular calibration ensures that devices maintain accuracy over time.
Documentation:
Detailed documentation is a crucial aspect of the calibration process. Calibration information embody information such because the date of calibration, gear used, calibration requirements, adjustments made, and the technician's signature.
Calibration Certificates:
Calibration labs provide certificates after the calibration course of. These certificates document the as-found and as-left conditions of the instrument, providing evidence of compliance with specified accuracy standards.
Adjustment and Repair:
If a process meter is discovered to be out of calibration, changes or repairs could also be necessary to deliver it again within the specified accuracy limits.
Calibration Tolerances:
Instruments have defined tolerances that specify the suitable vary of deviation from the true worth. Calibrations ensure that the instruments fall within these tolerances.
On-Site Calibration:
Some calibration actions can be performed on-site, decreasing the want to take away devices from the method. This is especially essential for important processes the place downtime ought to be minimized.
Calibration Management System:
Organizations could use a calibration management system to track and handle the calibration of their instruments. This system helps schedule and document calibration activities.
By adhering to these basics, industries can maintain the accuracy and reliability of their process meters, contributing to the general effectivity and safety of industrial processes. Regular calibration is important to satisfy high quality requirements and regulatory necessities..